The Ultimate Guide to Concrete Floor Coating Durability: Which Systems Last the Longest?
In this comprehensive guide, we’ll examine the science behind concrete floor coating durability, compare the longevity of different systems, and provide expert recommendations to help you make an informed decision.
Whether you’re considering a coating for your garage, commercial space, or industrial facility, this analysis of coating durability will help you identify which systems truly stand the test of time.
By the end, you’ll have a clear understanding of which concrete floor coating will provide the best long-term value for your specific needs.
Understanding Concrete Floor Coating Systems
Before diving into durability comparisons, it’s essential to understand what makes concrete floor coatings work. These specialized materials create a protective barrier over concrete surfaces, enhancing both functionality and aesthetics while extending the life of the underlying concrete.
The molecular structure of coating materials determines how well they adhere to concrete and resist wear over time.
High-quality coatings create strong chemical bonds with properly prepared concrete surfaces. This adhesion is critical for long-term performance.
Polyurea and polyaspartic coatings utilize advanced polymer technology that creates exceptionally strong cross-linked bonds. These chemical structures resist breaking down even under harsh conditions.
In contrast, acrylic sealers form weaker bonds that deteriorate more quickly when exposed to UV light, chemicals, and physical stress.
The thickness of the applied coating also significantly impacts durability.
Professional-grade systems typically apply multiple layers at specific thicknesses measured in mils (thousandths of an inch).
For example, industrial epoxy systems might be applied at 20-30 mils thickness, while basic acrylic sealers might only be 2-3 mils thick.
This substantial difference in material volume directly correlates to how long the coating will last before wearing through.
When exploring concrete floor coating options for your property in San Marcos, TX, understanding these fundamental principles will help you evaluate the various systems available.
Key Factors That Affect Coating Longevity
Several critical factors determine how long your concrete coating will last:
Surface preparation quality is perhaps the most crucial factor.
Even the most advanced coating will fail prematurely if applied to improperly prepared concrete.
Professional contractors like Grizzly Concrete Coating use diamond grinding and shot blasting to create the optimal surface profile for maximum adhesion.
Environmental conditions during application significantly impact coating performance.
Temperature and humidity levels must fall within specific ranges for proper curing.
Application outside these parameters can lead to adhesion failures, bubbling, or incomplete curing.
The concrete’s condition before coating also affects longevity.
Moisture issues, existing damage, or previous coatings can all compromise the new coating’s performance if not properly addressed during preparation.
Finally, the intended use of the space determines which coating system will provide optimal durability.
A residential garage floor faces different stresses than a commercial warehouse or an outdoor pool deck. Each environment requires specific coating properties to achieve maximum lifespan.
Comprehensive Durability Comparison: Ranking Coating Systems
When evaluating concrete floor coatings for longevity, it’s helpful to compare the major systems side by side. Here’s how the most common coating types rank in terms of durability.
Polyurea/Polyaspartic Systems (15-20 Year Lifespan)
Polyurea and polyaspartic coatings represent the pinnacle of concrete floor coating technology, offering the longest potential lifespan of 15-20 years with proper maintenance.
These advanced systems cure rapidly through a chemical reaction rather than evaporation, creating an exceptionally dense, cross-linked polymer structure.
The molecular composition of these coatings provides superior resistance to UV degradation, chemical exposure, and physical abrasion.
In high-traffic commercial environments, polyurea/polyaspartic systems have demonstrated remarkable durability, maintaining their appearance and protective properties years after installation.
According to industry testing, these systems can withstand up to 8,000 cycles on the Taber Abrasion Test before showing significant wear—far outperforming other coating types.
This exceptional wear resistance makes them ideal for demanding environments like automotive service centers, manufacturing facilities, and busy commercial kitchens.
For homeowners in Wimberley, TX seeking a truly long-term solution for garage floors, these premium systems offer the best return on investment despite their higher initial cost.
Industrial-Grade Epoxy Systems (10-15 Year Lifespan)
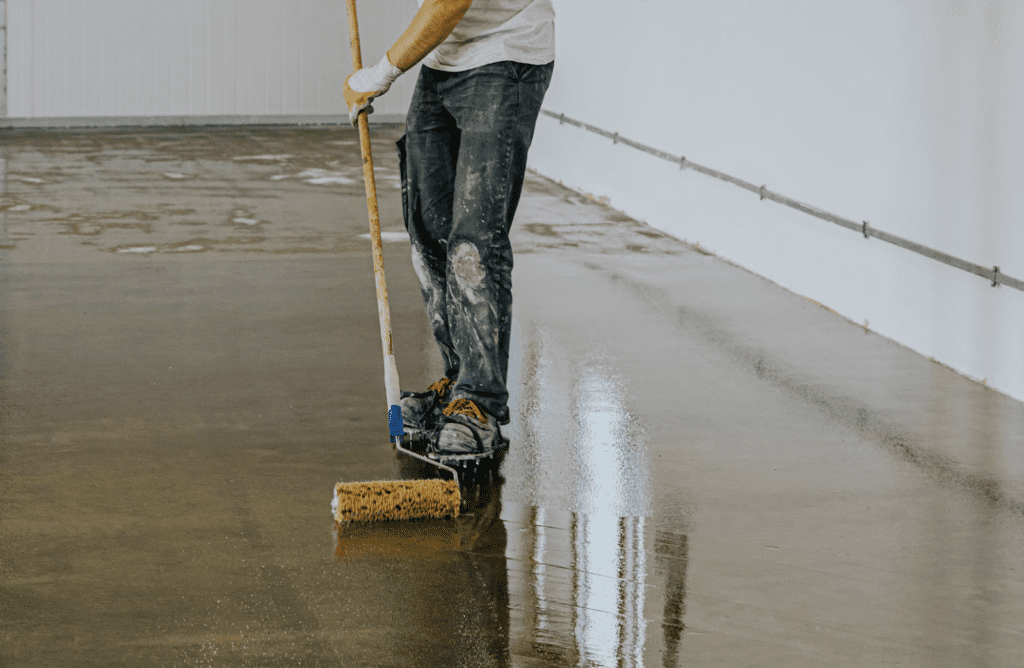
Industrial epoxy systems have been the workhorse of concrete floor coatings for decades, providing reliable performance with a typical lifespan of 10-15 years.
These two-component systems create a thick, durable surface through a chemical curing process that produces a hard, dense coating.
Modern epoxy formulations have improved significantly, with 100% solids epoxies offering superior thickness and durability compared to water-based alternatives.
At 20-30 mils thick, these coatings provide excellent resistance to impact, abrasion, and chemical exposure.
However, epoxies do have limitations. Most notably, they yellow and chalk when exposed to UV light, making them less suitable for outdoor applications.
They also have longer cure times than polyurea/polyaspartic systems, which can extend installation timelines.
For commercial and industrial facilities in Kyle, TX, epoxy systems continue to offer an excellent balance of performance and value, particularly for indoor applications where UV exposure isn’t a concern.
Urethane Coatings (8-12 Year Lifespan)
Urethane concrete coatings occupy the middle ground in durability, typically lasting 8-12 years before requiring significant maintenance or replacement.
These coatings offer excellent chemical resistance and UV stability, making them suitable for both indoor and outdoor applications.
Urethane coatings are often used as topcoats over epoxy systems to enhance UV resistance and provide additional chemical protection.
This combination leverages the strengths of both materials—the thickness and impact resistance of epoxy with the UV stability and chemical resistance of urethane.
The flexibility of urethane coatings also makes them more resistant to cracking in environments with temperature fluctuations.
This property is particularly valuable for facilities in Spring Branch, TX, where seasonal temperature changes can stress more rigid coating systems.
While not as durable as polyurea/polyaspartic systems, quality urethane coatings provide reliable performance at a more moderate price point, making them popular for commercial applications with moderate traffic and exposure.
Acrylic Sealers (2-5 Year Lifespan)
At the lower end of the durability spectrum, acrylic sealers typically last only 2-5 years before requiring reapplication.
These water-based or solvent-based products form a thin protective film on the concrete surface rather than creating a thick, structural coating.
Acrylic sealers are primarily designed to enhance appearance and provide minimal protection against staining and water penetration.
Their thin application (typically 2-3 mils) means they wear through quickly in areas with foot or vehicle traffic.
While they offer the advantage of easy application and low initial cost, their short lifespan makes them less economical over time.
Property owners often find themselves reapplying acrylic sealers every few years, with cumulative costs eventually exceeding those of more durable systems.
For light-duty applications or temporary protection, acrylic sealers may be appropriate. However, for most residential and commercial applications in Dripping Springs, TX, investing in a more durable coating system will provide better long-term value.
Environmental Factors Affecting Coating Durability
The environment where your concrete coating is installed plays a crucial role in determining its actual lifespan. Even the most durable systems can degrade prematurely when exposed to harsh conditions.
UV Exposure and Weathering Effects
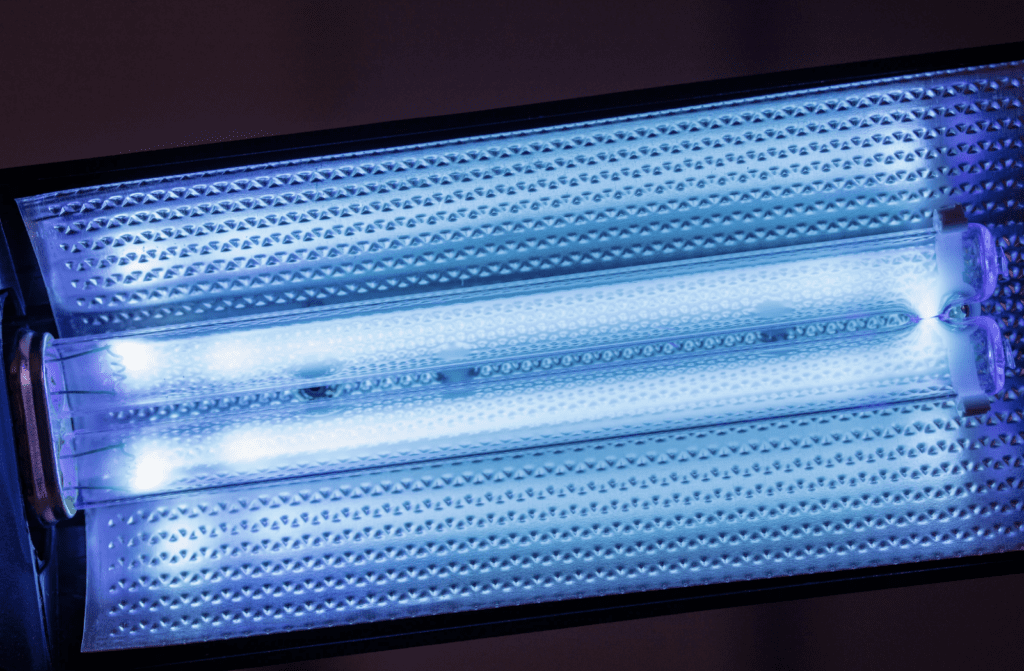
Ultraviolet radiation from sunlight is one of the most destructive forces affecting coating durability. UV exposure breaks down the chemical bonds in coating materials, leading to color fading, chalking, and eventual coating failure.
Polyurea/polyaspartic systems and urethane coatings offer the best UV resistance, maintaining their appearance and protective properties even with direct sun exposure. In contrast, epoxy coatings yellow significantly when exposed to UV light, often showing noticeable changes within months of outdoor installation.
In regions with intense sunlight like Marble Falls, TX, UV resistance becomes an even more critical factor when selecting a coating system for outdoor applications or spaces with significant natural light.
Temperature fluctuations also accelerate coating degradation through expansion and contraction cycles. Coatings with greater flexibility, like polyurea and urethane, accommodate these movements better than rigid systems like epoxy.
Chemical Exposure Resistance Comparison
Different coating systems vary dramatically in their resistance to chemicals, from household cleaners to industrial solvents and acids. This resistance directly impacts longevity in environments where chemical exposure is common.
The chemical resistance of your concrete floor coating is often the determining factor in its functional lifespan, especially in industrial and commercial settings where exposure to harsh substances is inevitable.
Polyurea coatings demonstrate exceptional resistance to a broad spectrum of chemicals, including acids, bases, solvents, and petroleum products. This comprehensive protection makes them ideal for automotive facilities, manufacturing plants, and laboratories.
Epoxy systems offer good chemical resistance but can be vulnerable to certain acids and solvents. Urethane coatings provide excellent protection against many chemicals but may soften when exposed to certain solvents.
For facilities where chemical exposure is a concern, professional coating contractors can provide detailed chemical resistance charts to help select the appropriate system based on specific exposure risks.
Impact and Abrasion Resistance Testing Results
The ability to withstand physical wear is essential for coating longevity, particularly in high-traffic areas. Industry-standard testing methods like the Taber Abrasion Test provide quantifiable data on how different coatings perform under controlled wear conditions.
According to 2024 testing data, polyurea/polyaspartic systems typically show less than 10 mg of weight loss after 1,000 cycles on the Taber Abrasion Test. High-quality epoxies average 50-75 mg loss, while acrylic sealers can lose 100-150 mg under the same conditions.
Impact resistance is equally important, especially in environments where dropped tools, equipment, or materials are common. Polyurea coatings can withstand direct impacts that would chip or crack more brittle systems like epoxy.
These performance differences translate directly to real-world durability. In high-traffic commercial environments, premium polyurea systems often maintain their integrity for years, while lesser coatings show visible wear paths and damage within months.
Application-Specific Durability Recommendations
Different environments place unique demands on concrete floor coatings. Understanding these specific requirements helps in selecting the most durable system for each application.
Residential Garage Floors: Best Long-Term Options
For residential garage floors, the combination of vehicle traffic, chemical exposure from automotive fluids, and occasional heavy impacts creates a challenging environment for floor coatings. The most durable option for this application is a polyurea/polyaspartic system with a minimum thickness of 20 mils.
These premium systems resist hot tire pickup (a common failure point for lesser coatings), chemical staining from automotive fluids, and impact damage from dropped tools. While the initial investment is higher than basic epoxy or acrylic options, the extended lifespan of 15-20 years makes them more economical over time.
For homeowners seeking the best balance of performance and value, hybrid systems that combine an epoxy base coat with a polyaspartic topcoat offer excellent durability at a moderate price point. These systems typically provide 10-15 years of service in residential garage applications.
Homeowners in Bulverde, TX should consider the specific demands of their garage environment, including vehicle type, frequency of use, and exposure to elements when selecting a coating system.
Commercial and Industrial Environments
Commercial and industrial facilities face the most demanding conditions for floor coatings, with heavy equipment traffic, potential chemical exposure, and continuous use. In these environments, coating failure can lead to significant operational disruptions and safety hazards.
For manufacturing facilities, warehouses, and distribution centers, industrial-grade polyurea systems provide the best long-term performance. These coatings maintain their integrity even under constant forklift traffic and resist damage from dropped materials and equipment.
Food processing facilities and commercial kitchens require coatings that can withstand thermal shock, chemical cleaning agents, and constant moisture. Specialized polyurea systems designed for these environments offer superior performance, with antimicrobial properties that support hygiene requirements.
For retail and commercial spaces in Canyon Lake, TX, where aesthetics are as important as durability, decorative polyaspartic systems provide the perfect combination of long-term performance and visual appeal.
Outdoor and Exposed Concrete Surfaces
Outdoor concrete surfaces present unique durability challenges due to UV exposure, freeze-thaw cycles, and moisture penetration. For these applications, UV-stable polyaspartic and urethane coatings offer the best long-term performance.
Pool decks, patios, and walkways benefit from textured polyaspartic systems that provide slip resistance along with durability. These coatings maintain their appearance and protective properties even with constant sun exposure and periodic moisture.
For commercial exterior applications like parking garages and loading docks, traffic-grade polyurea systems with enhanced flexibility accommodate structural movement while resisting wear from vehicle traffic. These specialized coatings typically provide 10-15 years of service even in these demanding environments.
Outdoor concrete surfaces in New Braunfels, TX face particular challenges from intense summer heat and occasional freezing temperatures, making coating selection especially important for long-term performance.
Installation Methods That Maximize Durability
Even the highest quality coating materials will fail prematurely if not properly installed. Professional installation techniques significantly impact the ultimate durability of any concrete floor coating system.
Surface Preparation: The Foundation of Longevity
Surface preparation is unquestionably the most critical factor in coating durability. Industry studies consistently show that over 80% of coating failures can be traced back to inadequate surface preparation.
Professional preparation methods like diamond grinding and shot blasting create the optimal surface profile for maximum coating adhesion. These processes remove surface contaminants and create microscopic peaks and valleys that allow the coating to mechanically bond with the concrete substrate.
Moisture testing is another essential preparation step often overlooked in DIY applications. Excess moisture vapor transmission through concrete can cause coating delamination and failure. Professional contractors use calcium chloride testing and relative humidity probes to identify potential moisture issues before coating application.
Proper crack and joint treatment also impacts long-term durability. Professional installation includes appropriate repair of cracks and treatment of control joints to prevent these weak points from compromising the coating system.
Professional vs DIY Application: Durability Implications
The gap between professional and DIY coating application is substantial when measuring long-term durability.
Professional contractors bring specialized equipment, extensive training, and product-specific expertise that directly translates to coating longevity.
Professional application equipment ensures consistent mixing ratios, proper material temperature control, and even application thickness—all factors that significantly impact coating performance.
Commercial-grade sprayers, squeegees, and rollers allow for precise application that DIY tools cannot match.
Temperature and humidity control during application is another advantage of professional installation.
Experienced contractors monitor environmental conditions and adjust application techniques accordingly, ensuring optimal curing conditions for maximum coating performance.
For property owners in Boerne, TX seeking the longest-lasting concrete floor coating, professional installation by experienced contractors provides significantly better durability than DIY alternatives.
Multi-Layer Systems for Extended Lifespan
The most durable concrete floor coatings utilize multi-layer application techniques that maximize both protection and longevity. These systems typically include:
A primer layer that penetrates the concrete surface to create a strong foundation for subsequent layers. This critical layer addresses porosity issues and enhances adhesion.
A build coat (or multiple build coats) that provides the main body and protection of the coating system. This layer delivers impact resistance, chemical protection, and the primary durability characteristics.
A topcoat that seals the system and provides specific performance properties like UV resistance, chemical protection, or enhanced abrasion resistance. This final layer is often the first line of defense against wear and damage.
Each layer in a multi-coat system serves a specific purpose, and the combined performance exceeds what any single layer could provide.
Professional contractors carefully control the application timing between layers to ensure optimal chemical bonding, creating a monolithic coating system with superior durability.
Maintenance Protocols for Maximum Coating Life
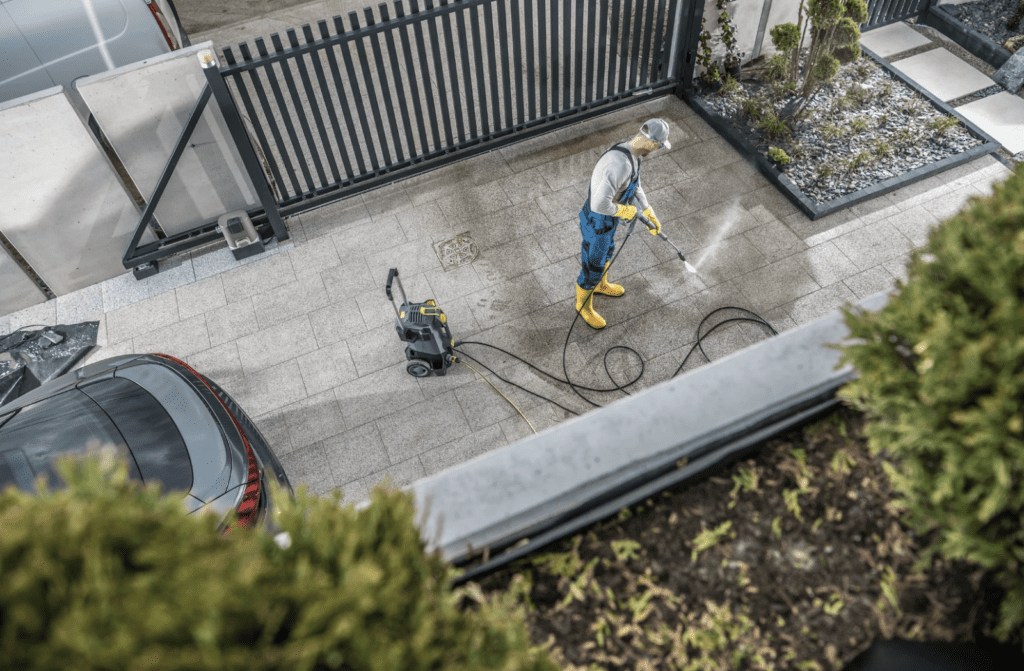
Cleaning Techniques That Preserve Coating Integrity
Regular cleaning is essential for maintaining coating appearance and preventing premature wear. However, using inappropriate cleaning methods can damage coatings and reduce their lifespan.
For routine maintenance, microfiber dust mops and pH-neutral cleaners are ideal for removing surface dirt without damaging the coating. Avoid harsh chemicals, acidic cleaners, and abrasive scrubbing pads that can etch or scratch the coating surface.
For more thorough cleaning, auto scrubbers with non-abrasive pads provide excellent results in commercial environments.
In residential settings, soft-bristle brushes and gentle pressure washing (under 1500 PSI) can safely remove stubborn dirt without compromising the coating.
Prompt attention to spills, particularly chemicals and automotive fluids, prevents staining and potential coating damage. Even highly chemical-resistant coatings benefit from timely cleanup of aggressive substances.
Preventative Maintenance Schedule by Coating Type
Different coating systems require specific maintenance approaches to maximize their lifespan. Following a coating-specific maintenance schedule ensures optimal long-term performance.
For polyurea/polyaspartic systems, annual professional inspections help identify and address any potential issues before they lead to coating failure. These premium systems generally require minimal maintenance beyond regular cleaning.
Epoxy systems benefit from reapplication of a thin maintenance coat every 5-7 years in high-traffic areas. This refreshes the surface appearance and restores protective properties without requiring complete system replacement.
Urethane coatings typically need maintenance coats every 3-5 years, particularly in outdoor applications where UV exposure accelerates degradation. This periodic renewal extends the functional lifespan of the system significantly.
Acrylic sealers require the most frequent maintenance, with reapplication recommended every 1-2 years to maintain protection. This ongoing maintenance requirement should be factored into the total lifecycle cost when comparing coating options.
When and How to Perform Coating Repairs
Even well-maintained coatings may eventually require repairs due to impacts, substrate movement, or localized wear. Addressing these issues promptly prevents more extensive damage and extends overall coating life.
Small chips and scratches can often be repaired with touch-up kits provided by coating manufacturers.
These repairs are most successful when performed soon after the damage occurs, before contamination of the damaged area.
For more significant damage, professional repair techniques include partial removal of the damaged section and seamless integration of new coating material.
These repairs, when properly executed, restore both the protective properties and appearance of the coating.
End-of-life rejuvenation options include aggressive cleaning and application of a compatible topcoat to extend service life. This approach is particularly effective for structurally sound coatings that have lost their aesthetic appeal or surface protection.
For specific advice on maintaining your concrete floor coating, the experts at Grizzly Concrete Coating can provide customized recommendations based on your coating type and usage conditions.
Your Concrete Coating Investment: Making the Right Choice
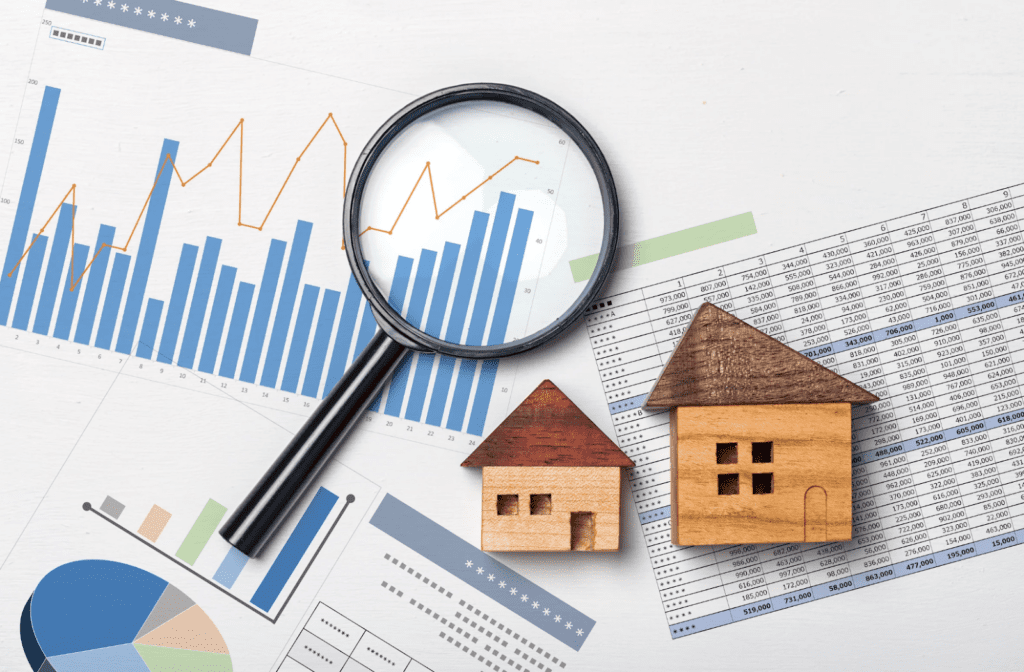
When evaluating concrete floor coating options, considering both initial costs and long-term value provides the clearest picture of which system truly offers the best investment.
The most durable coating systems—polyurea and polyaspartic—typically cost 2-3 times more than basic acrylic sealers initially. However, when analyzed over a 20-year period, these premium systems often prove more economical due to their extended lifespan and reduced maintenance requirements.
For example, a premium polyaspartic garage floor coating might cost $6-8 per square foot initially but last 15-20 years with minimal maintenance. In contrast, an acrylic sealer at $1-2 per square foot might require reapplication every 2-3 years, resulting in significantly higher cumulative costs over the same period.
Commercial and industrial facilities benefit even more from investing in durable coating systems, as the operational disruption and labor costs associated with frequent recoating can far exceed the material cost differences between coating types.
For property owners seeking specific guidance on the most cost-effective coating solution for their needs, consulting with experienced professionals from Grizzly Concrete Coating provides valuable insights tailored to your specific application and budget considerations.
Frequently Asked Questions
How long should a professional concrete floor coating last?
Professional concrete floor coatings vary in longevity depending on the system used.
Premium polyurea/polyaspartic systems typically last 15-20 years in residential applications and 10-15 years in commercial settings with proper maintenance.
Industrial-grade epoxy systems generally provide 10-15 years of service, while urethane coatings last 8-12 years. Basic acrylic sealers have the shortest lifespan at just 2-5 years before requiring reapplication.
Factors affecting actual longevity include installation quality, surface preparation, environmental conditions, and maintenance practices.
For the longest-lasting results, professional installation by experienced contractors is essential, as proper surface preparation and application techniques significantly impact coating durability.
What causes concrete floor coatings to fail prematurely?
Premature coating failure typically stems from several key factors.
Poor surface preparation is the leading cause, accounting for approximately 80% of all coating failures.
Inadequate concrete profiling, failure to address moisture issues, and improper cleaning before application prevent proper adhesion.
Incorrect mixing ratios and improper application techniques also lead to early failure, particularly with two-component systems that require precise proportioning.
Environmental conditions during installation, including temperature and humidity outside the manufacturer’s recommended ranges, can prevent proper curing.
Excessive moisture vapor transmission through the concrete substrate often causes delamination and bubbling.
Finally, using the wrong coating system for the environment (such as epoxy in UV-exposed areas) inevitably leads to accelerated degradation and premature failure.
Are DIY concrete coating kits as durable as professional systems?
DIY concrete coating kits typically offer significantly lower durability than professional systems.
Most retail and online DIY kits use lower-solids content formulations that result in thinner application (3-10 mils versus 20+ mils for professional systems). These thinner coatings wear through more quickly under normal use.
DIY kits also lack the specialized primers and topcoats that enhance professional system performance.
The preparation equipment available to homeowners (like rental grinders) cannot achieve the same surface profile as professional diamond grinding and shot blasting equipment, resulting in weaker adhesion.
Additionally, professional installers bring experience in environmental assessment, moisture testing, and application techniques that directly impact longevity.
While DIY kits may save money initially, they typically provide only 20-40% of the lifespan of professionally installed systems.
How does climate affect concrete coating durability?
Climate conditions significantly impact concrete coating durability through several mechanisms.
In hot, sunny regions, UV radiation degrades most coating types, with epoxies being particularly vulnerable to yellowing and chalking. Polyaspartic and urethane systems offer superior UV resistance.
Areas with freeze-thaw cycles create expansion and contraction stresses that can crack rigid coatings like epoxy. More flexible systems like polyurea better accommodate these movements.
High-humidity regions face increased risks of moisture vapor transmission through concrete, potentially causing coating delamination.
Professional moisture testing and appropriate moisture mitigation systems are essential in these areas.
Coastal environments expose coatings to salt spray, which can penetrate and degrade lesser-quality systems.
For properties in regions with extreme climate conditions, consulting with local coating professionals familiar with regional challenges ensures selecting the most durable system for your specific climate.
What maintenance extends the life of concrete floor coatings?
Implementing a proper maintenance routine significantly extends concrete coating lifespan.
Regular cleaning with pH-neutral cleaners prevents dirt accumulation that can abrade the surface over time. Avoid harsh chemicals, bleach, and ammonia-based products that can etch or dull the finish.
Place protective pads under furniture legs and heavy equipment to prevent concentrated pressure points.
Clean spills promptly, especially chemicals, automotive fluids, and acidic substances that can damage the coating surface.
For commercial floors, implement entrance matting systems to capture abrasive particles before they’re tracked onto coated surfaces.
Schedule periodic professional inspections to identify and address minor issues before they lead to coating failure.
Apply refresher coats as recommended by the manufacturer—typically every 5-7 years for high-traffic areas with premium systems.
This maintenance coat restores the protective properties and appearance without requiring complete system replacement, significantly extending the overall coating lifespan.
About Grizzly Concrete Coating
Grizzly Concrete Coating is a premier provider of high-performance concrete floor coating solutions serving San Marcos, Wimberley, Kyle, Spring Branch, Dripping Springs, Marble Falls, Bulverde, Canyon Lake, New Braunfels, Boerne, and surrounding Texas communities.
With a focus on durability and quality craftsmanship, our team specializes in polyurea, polyaspartic, and epoxy coating systems for residential, commercial, and industrial applications.We pride ourselves on using only the highest quality materials and employing industry-best installation techniques to ensure maximum coating longevity. Visit our website or explore our frequently asked questions.
No responses yet