Commercial vs. Residential Concrete Coatings: Understanding the Key Differences
When it comes to protecting and enhancing concrete surfaces, the type of coating you choose matters significantly. Whether you’re a homeowner looking to upgrade your garage floor or a business owner needing durable flooring for your commercial space, understanding the differences between commercial and residential concrete coatings is essential.
These specialized treatments not only improve the appearance of concrete but also extend its lifespan and functionality in dramatically different ways, depending on the setting.
In this comprehensive guide, we’ll explore the key differences between commercial and residential concrete coatings, examining everything from durability requirements and application processes to cost considerations and maintenance needs.
By the end, you’ll have the knowledge to make an informed decision about the right concrete coating solution for your specific needs.
Introduction to Concrete Coating Systems
Concrete coatings have evolved significantly over the past decade, transforming from simple sealers to sophisticated systems that can dramatically enhance both the appearance and performance of concrete surfaces.
These coating systems serve multiple purposes: they protect the underlying concrete from damage, improve aesthetic appeal, and add functionality to otherwise plain surfaces.
At their core, concrete coatings create a protective barrier that shields concrete from moisture penetration, chemical spills, UV damage, and physical wear.
However, the specific formulations and application methods vary widely between residential and commercial settings due to their different performance requirements.
According to industry research from 2024, the global concrete coating market continues to grow at approximately 6.8% annually, driven by innovations in coating technology and increasing awareness of concrete protection benefits.
This growth spans both the residential sector, where homeowners seek attractive, low-maintenance solutions, and the commercial sector, where durability and compliance with safety standards are paramount.
The right concrete coating doesn’t just protect your investment—it transforms an ordinary surface into a functional, beautiful asset that adds value to your property for years to come.
Before diving into the specific differences, it’s important to understand that concrete coatings generally fall into several major categories: epoxy, polyurea, polyaspartic, urethane, and acrylic systems.
Each has distinct properties that make them suitable for different applications, and the choice between them depends largely on whether they’re being used in a residential or commercial context.
Residential Concrete Coatings: Features and Benefits
Residential concrete coatings are specifically designed to meet the needs of homeowners who want to enhance their living spaces while maintaining a balance between aesthetics, durability, and cost. These coatings are formulated to withstand typical household conditions while providing an attractive finish that complements home décor.
The primary focus of residential concrete coatings often leans toward aesthetic appeal and moderate durability. Homeowners typically prioritize appearance, ease of cleaning, and resistance to common household chemicals.
According to a 2024 homeowner survey, 78% of respondents ranked appearance as their top consideration when selecting a concrete coating for their home.
Residential coatings generally need to withstand foot traffic, occasional vehicle traffic (in garages), furniture movement, and typical household spills. While they must be durable, they don’t require the extreme impact and chemical resistance that commercial environments demand.
Common Applications in Residential Settings
In residential settings, concrete coatings are most commonly applied to:
- Garage floors, where they provide protection against automotive fluids, salt, and tire marks
- Basement floors, where moisture resistance and improved lighting reflection are valuable
- Patios and pool decks, where slip resistance and UV stability are crucial
- Driveways, where resistance to weather conditions and automotive fluids is important
- Interior living spaces, where decorative concrete has become increasingly popular
For instance, concrete pool deck coating in Spring Branch TX has become increasingly popular as homeowners recognize the value of protecting these high-exposure areas from sun damage, chlorine, and constant moisture.
Aesthetic Considerations for Home Environments
Residential concrete coatings offer extensive customization options to complement home décor. Homeowners can choose from various colors, patterns, and finishes, including:
- Solid colors that coordinate with interior or exterior design schemes
- Decorative flake or chip systems that create a terrazzo-like appearance
- Metallic epoxy finishes that produce unique, flowing patterns
- Stained concrete that mimics natural stone or creates artistic effects
The aesthetic flexibility of residential coatings allows homeowners to create personalized spaces that reflect their taste while maintaining functionality. Many residential concrete coating services now offer visualization tools to help homeowners preview different options before making a decision.
Durability Requirements for Residential Use
While residential coatings don’t need the extreme durability of commercial applications, they still must withstand daily household activities. A quality residential concrete coating should last 5-10 years with proper maintenance, depending on the specific product and exposure conditions.
Residential coatings typically feature:
- Moderate chemical resistance to household cleaners and automotive fluids
- Scratch and abrasion resistance for furniture movement
- UV stability for outdoor applications
- Moisture resistance to prevent mold and mildew growth
For areas like driveways that experience more intense use, specialized solutions like concrete driveway coating in Spring Branch TX provide enhanced durability while maintaining residential-appropriate aesthetics.
Commercial Concrete Coatings: Performance and Functionality
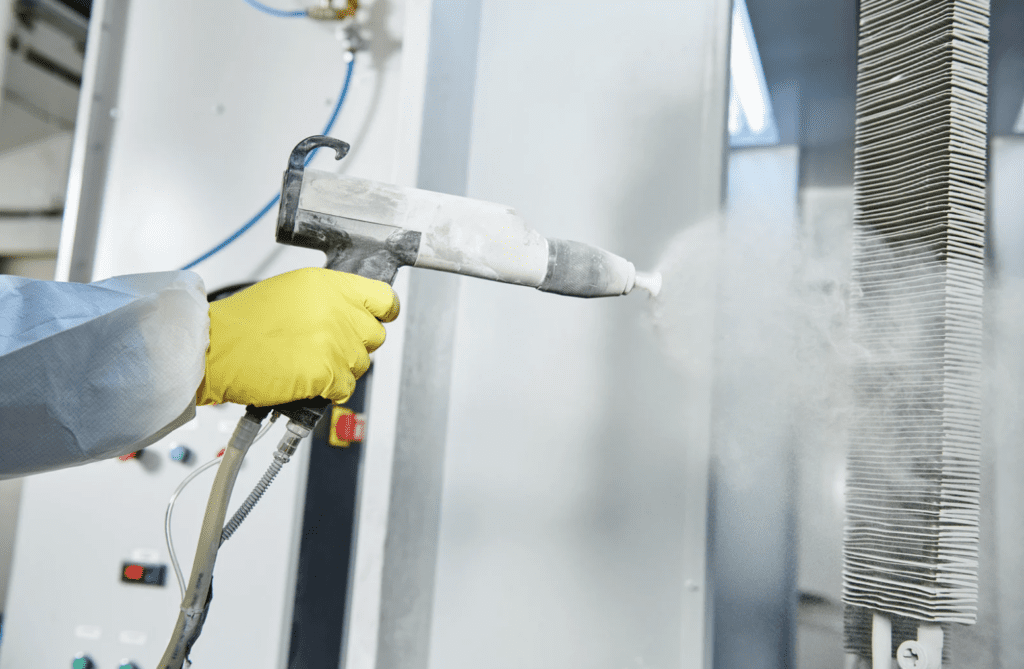
Commercial concrete coatings are engineered to withstand significantly more demanding conditions than their residential counterparts. These high-performance systems prioritize durability, safety, and longevity in environments that experience heavy traffic, chemical exposure, and constant use.
The primary focus of commercial concrete coatings is functionality and performance under extreme conditions. Business owners and facility managers typically prioritize durability, safety compliance, maintenance requirements, and long-term cost-effectiveness over purely aesthetic considerations.
According to industry data from 2025, commercial-grade concrete coatings can extend floor life by up to 300% compared to uncoated concrete, representing significant cost savings over time for businesses.
This performance difference explains the higher initial investment that commercial coatings typically require.
High-Traffic Area Solutions
Commercial environments experience foot and vehicle traffic volumes that far exceed residential settings. Retail spaces might see thousands of customers daily, while warehouses contend with constant forklift traffic and heavy equipment movement.
Commercial concrete coatings for high-traffic areas typically feature:
- Extreme abrasion resistance to prevent wearing paths
- Impact resistance for dropped tools and equipment
- Thicker application profiles (often 15-30 mils compared to 8-12 mils for residential)
- Rapid cure formulations to minimize business downtime
Commercial concrete coating services specialize in creating solutions that can withstand these demanding conditions while minimizing the frequency of repairs and reapplications.
Safety and Compliance Requirements
Commercial concrete coatings must meet stringent safety and regulatory requirements that don’t typically apply to residential installations. These include:
- Slip resistance ratings that comply with ADA and OSHA standards
- Fire resistance ratings for certain building codes
- VOC compliance with local and federal regulations
- Chemical resistance profiles specific to the industry (food service, manufacturing, etc.)
For public-facing areas like entryways, specialized solutions such as concrete entryway coating in Spring Branch TX must balance safety requirements with aesthetic appeal to create a positive first impression while ensuring code compliance.
Branding and Aesthetic Opportunities
While performance is paramount, commercial concrete coatings also offer branding and aesthetic opportunities for businesses.
Modern commercial coatings can incorporate:
- Company colors and logos embedded in the floor design
- Directional markings and safety indicators
- Zone demarcation for different operational areas
- Decorative elements that enhance customer experience
These aesthetic elements must be achieved without compromising the performance characteristics of the coating system.
For example, a restaurant might use a decorative yet highly chemical-resistant coating in customer areas while opting for a more utilitarian but extremely durable system in kitchen areas.
Material Comparison: Polyurea vs. Epoxy vs. Urethane
Understanding the different materials used in concrete coatings is crucial for selecting the right system for either commercial or residential applications.
Performance Characteristics
Epoxy Coatings: Traditionally the most common coating type, epoxies offer excellent adhesion to concrete and good chemical resistance.
They’re available in various forms:
- Standard epoxy: Good for residential use with moderate durability
- 100% solids epoxy: Higher build, better durability for commercial applications
- Water-based epoxy: Lower VOCs but typically less durable
Polyurea Coatings: Featuring rapid cure times and excellent flexibility, polyurea has gained popularity in both sectors:
- Extremely fast cure (minutes rather than hours)
- Superior flexibility and crack-bridging capability
- Excellent chemical and abrasion resistance
- UV stable formulations available
Urethane Coatings: Often used as topcoats over epoxy systems:
- Superior UV resistance compared to epoxy
- Better chemical resistance than epoxy alone
- More flexible than epoxy, reducing cracking potential
- Available in aliphatic formulations for color stability
Epoxy floor contractors in Spring Branch TX, often recommend hybrid systems that combine the benefits of multiple materials. For example, an epoxy base coat with a polyaspartic or urethane topcoat can achieve optimal performance.
Cost-Benefit Analysis
The cost differential between coating materials can be substantial but must be evaluated in terms of lifetime value:
- Epoxy systems: Generally, the most economical initial investment ($3-7 per square foot for residential, $5-12 for commercial)
- Polyurea systems: Higher initial cost ($7-12 for residential, $10-18 for commercial) but faster installation and potentially longer lifespan
- Urethane systems: Often used as topcoats, adding $1-3 per square foot to system cost but extending performance significantly
Commercial applications typically justify the higher material costs due to the reduced frequency of replacement and the operational costs associated with facility downtime during reapplication.
Lifespan and Warranty Expectations
Warranty periods vary significantly between residential and commercial applications, reflecting the different performance expectations:
- Residential epoxy systems: Typically 2-5 year warranties
- Residential polyurea/polyaspartic systems: Often 5-10 year warranties
- Commercial epoxy systems: Usually 1-3 year warranties (due to higher wear expectations)
- Commercial polyurea systems: Generally 3-7 year warranties
The shorter warranty periods for commercial applications don’t necessarily indicate inferior products, but rather reflect the more demanding conditions these coatings face. Many concrete floor coating contractors offer extended warranty options for both residential and commercial clients with proper maintenance programs.
Installation Process Differences
The installation process for concrete coatings differs significantly between residential and commercial projects, affecting everything from preparation methods to curing times and project scheduling.
Surface Preparation Requirements
Surface preparation is critical for coating adhesion and long-term performance in both sectors, but the methods and standards vary.
Residential Preparation:
- Diamond grinding or shot blasting to CSP (Concrete Surface Profile) 1-2
- Crack repair using epoxy fillers
- Minor leveling to address unevenness
- Typically 1-2 days of preparation for an average project
Commercial Preparation:
- More aggressive shot blasting to CSP 3-5
- Extensive crack repair and joint treatment
- Often requires significant leveling and patching
- May include moisture mitigation systems
- Typically requires 2-4 days of preparation for an average project
The more rigorous preparation for commercial projects reflects the higher performance demands and the greater consequences of coating failure in these environments.
Application Techniques
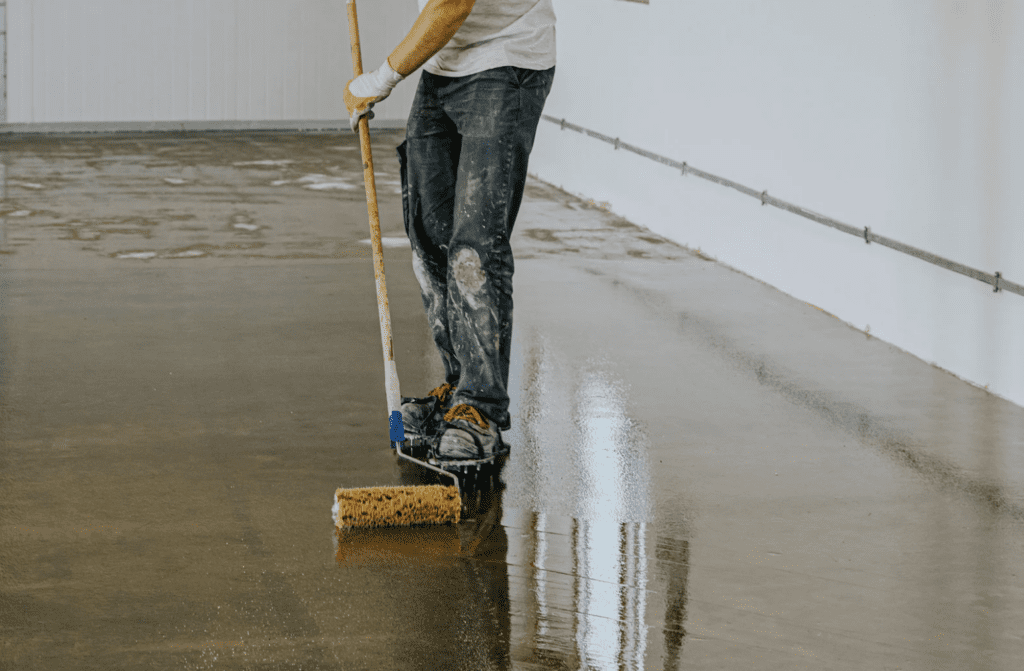
Application methods also differ between sectors:
Residential Application:
- Often applied by smaller crews (2-3 technicians)
- Typically applied with rollers and squeegees
- Usually involves 2-3 coating layers
- Often completed in 2-3 days total
Commercial Application:
- Larger crews (4-8 technicians) for efficiency
- May use power trowels, spray equipment, or specialized applicators
- Often involves 3-5 coating layers, including primers and topcoats
- May require phased installation to maintain business operations
- Typically completed in 3-7 days, depending on size
For specialized applications like concrete sidewalk coating in Spring Branch TX, techniques may be adapted to address outdoor conditions and public access requirements.
Curing and Downtime Considerations
Curing times and the associated downtime represent one of the most significant practical differences between residential and commercial coating projects:
Residential Curing Considerations:
- Homeowners can typically vacate the area during installation
- Standard epoxy systems require 24-72 hours before foot traffic
- Full cure and vehicle traffic often require 5-7 days
- Scheduling is relatively flexible
Commercial Curing Considerations:
- Business operations must often continue during installation
- Fast-cure systems (polyaspartic/polyurea) are frequently used to minimize downtime
- Return to service may be measured in hours rather than days
- Installation often occurs during off-hours (nights/weekends)
- Phased installation approaches to maintain partial operation
Maintenance Requirements and Long-Term Care
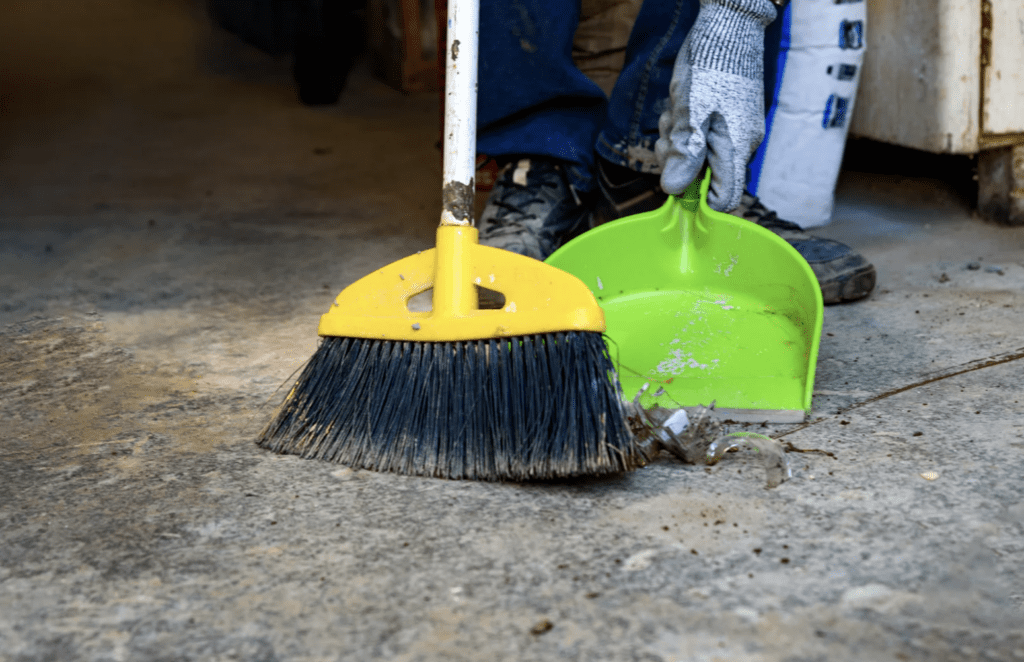
Proper maintenance is essential for maximizing the lifespan of concrete coatings in both residential and commercial settings, though the specific protocols differ substantially.
Residential Maintenance Protocols
Residential concrete coatings typically require relatively simple maintenance routines:
- Regular sweeping and dust mopping to remove abrasive particles
- Weekly cleaning with pH-neutral cleaners
- Avoiding harsh chemicals like bleach or ammonia
- Annual inspection for damage or wear
- Reapplication of topcoat every 3-5 years in high-use areas
Homeowners seeking concrete coating services in Spring Branch TX, often receive detailed maintenance instructions as part of their installation package to ensure optimal performance.
Commercial Maintenance Schedules
Commercial maintenance is more intensive and systematic:
- Daily cleaning with auto-scrubbers or industrial equipment
- Specialized cleaning agents formulated for specific industries
- Weekly deep cleaning of high-traffic areas
- Conduct monthly inspections for damage, particularly in transition areas
- Scheduled reapplication of wear coats in high-traffic zones
- Documented maintenance programs for warranty compliance
Many commercial facilities implement maintenance contracts with their coating provider or a specialized maintenance company to ensure proper care and extend coating’s lifespan. This proactive approach typically results in lower lifetime costs despite the higher maintenance investment.
Environmental and Sustainability Considerations
Environmental factors have become increasingly important in both residential and commercial concrete coating selections, though the specific concerns and regulations differ between sectors.
VOC Content and Regulations
Volatile Organic Compound (VOC) regulations impact coating choices in both sectors:
Residential VOC Considerations:
- Homeowners increasingly request low-VOC options for health reasons
- Residential applications must comply with regional VOC limits
- Water-based systems are often preferred for interior residential applications
- Odor during installation is a significant concern for homeowners
Commercial VOC Considerations:
- Must comply with strict industrial VOC regulations
- May require specific documentation for LEED certification
- Often must meet industry-specific environmental standards
- May need to maintain production during installation, limiting VOC options
Concrete overlay contractors in Spring Branch TX have adapted to these evolving regulations by offering environmentally responsible options that don’t compromise performance.
Eco-Friendly Coating Options
Both sectors have seen growth in environmentally friendly coating options:
Residential Eco-Friendly Options:
- Bio-based epoxy systems derived from plant materials
- Water-based polyurethanes with minimal VOCs
- Recycled content in decorative aggregate systems
Commercial Eco-Friendly Options:
- High-solids formulations that reduce VOC content
- Rapidly renewable resource content
- Extended lifespan systems that reduce replacement frequency
- Energy-reflective coatings that reduce building cooling costs
These eco-friendly alternatives often command premium prices but can contribute to green building certifications and improved indoor air quality, making them increasingly popular in both markets.
Make Your Concrete Surfaces Work for You
When it comes to concrete coatings, the differences between commercial and residential applications are substantial and impact every aspect, from material selection to installation and maintenance. Understanding these differences is crucial for making informed decisions that balance performance needs, aesthetic preferences, and budget considerations.
For residential applications, the focus on aesthetic appeal, moderate durability, and reasonable cost makes systems like decorative epoxy or polyaspartic coatings ideal for transforming garages, basements, and outdoor living spaces. These coatings enhance your home’s beauty while providing practical benefits like easier cleaning and improved durability.
Commercial environments demand coatings that prioritize extreme durability, safety compliance, and minimal maintenance requirements. Polyurea, high-solids epoxy, and specialized urethane systems deliver the performance needed for these demanding applications, often with customization options that support branding and operational efficiency.
Grizzly Concrete Coatings specializes in both residential and commercial concrete coating applications, bringing expertise in material selection, professional installation, and long-term maintenance support. Our team understands the unique requirements of each sector and can help you navigate the options to find the perfect solution for your specific needs.
Ready to transform your concrete surfaces? Contact Grizzly Concrete Coatings today for a consultation and discover how our specialized coating systems can enhance your property’s appearance, functionality, and value for years to come. Don’t settle for ordinary concrete when you can have extraordinary performance and beauty with the right coating system.
Frequently Asked Questions
How long do concrete coatings typically last in commercial versus residential settings?
Residential concrete coatings typically last 5-10 years before requiring significant maintenance or reapplication, depending on the specific product used and exposure conditions. High-quality polyaspartic or polyurea systems in residential settings may extend this lifespan to 10-15 years with proper care.
In contrast, commercial concrete coatings generally have a shorter functional lifespan of 3-7 years due to the much higher traffic and abuse they receive. However, commercial systems are designed with this accelerated wear in mind, often incorporating sacrificial wear layers that can be reapplied without removing the entire system.
The actual lifespan in both settings depends heavily on factors like traffic volume, exposure to chemicals, maintenance practices, and the quality of the initial installation.
What makes commercial concrete coatings more expensive than residential options?
Commercial concrete coatings typically cost 30-50% more than residential systems due to several factors.
First, commercial coatings use higher solids content and specialty additives to achieve greater durability, chemical resistance, and safety features like enhanced slip resistance.
Second, commercial installations require more rigorous surface preparation, often including shot blasting to higher concrete surface profile (CSP) standards and moisture mitigation systems.
Third, commercial projects frequently require fast-cure formulations to minimize business downtime, and these rapid-cure materials command premium prices.
Finally, commercial coatings often involve more complex systems with multiple specialized layers (primers, build coats, broadcast layers, and topcoats) compared to the simpler 2-3 layer systems typical in residential applications.
Can I use a residential concrete coating in a light commercial setting to save money?
While it may be tempting to use residential concrete coatings in light commercial settings to reduce costs, this approach often leads to premature failure and higher long-term expenses.
Even “light” commercial environments typically experience 5-10 times the foot traffic of residential spaces, plus additional stresses from equipment, rolling loads, and more frequent cleaning.
However, there are middle-ground options for spaces with moderate use.
Some manufacturers offer “commercial-light” formulations designed specifically for environments like small offices, boutique retail, or low-traffic professional services. These provide enhanced durability over residential products while avoiding the full cost of heavy-duty commercial systems.
Consult with a professional coating contractor who can assess your specific traffic patterns and recommend an appropriate system that balances initial cost with long-term performance.
How do maintenance requirements differ between commercial and residential concrete coatings?
Maintenance requirements differ significantly between sectors.
Residential coatings typically require simple care: regular sweeping, weekly cleaning with pH-neutral cleaners, and annual inspections. Recoating is usually needed every 3-5 years in high-use areas.
Commercial maintenance is more intensive, requiring daily cleaning with specialized equipment, weekly deep cleaning of high-traffic zones, monthly professional inspections, and documented maintenance programs for warranty compliance.
Commercial settings often implement scheduled reapplication of wear coats in high-traffic areas every 12-24 months.
The more rigorous commercial maintenance reflects both the higher performance demands and the greater financial consequences of coating failure in business environments. Many commercial facilities establish maintenance contracts to ensure proper care protocols are followed consistently.
Are there concrete coating options that work well in both residential and commercial applications?
Yes, certain concrete coating systems bridge the gap between residential and commercial applications effectively.
Polyaspartic coatings have gained popularity in both sectors due to their excellent balance of properties: they offer the durability needed for light commercial use while providing the aesthetic options homeowners desire.
High-quality polyurea systems similarly work well in both environments, offering excellent chemical resistance, flexibility, and rapid cure times.
These crossover systems typically feature UV stability, good chemical resistance, and decorative options like color flakes or metallic effects.
They’re particularly suitable for residential garages that see heavier use, home-based businesses, boutique retail spaces, and professional offices.
While these versatile systems command higher prices than basic residential epoxies, they offer excellent value through extended lifespan and enhanced performance in both settings.
About Grizzly Concrete Coatings
Grizzly Concrete Coatings is a premier provider of high-performance concrete coating solutions serving both residential and commercial clients throughout Texas.
With locations in Spring Branch, Leander, Liberty Hill, and surrounding areas, our team brings decades of combined experience in concrete preparation, coating application, and long-term maintenance services.
We specialize in custom coating solutions using the latest polyaspartic, polyurea, and epoxy technologies to deliver exceptional durability and stunning aesthetics.
Our commitment to quality craftsmanship, transparent pricing, and exceptional customer service has earned us a reputation as the region’s trusted concrete coating experts.Visit our website or check our reviews to learn why so many homeowners and businesses choose Grizzly Concrete Coatings for their flooring needs.
No responses yet